ゲートサイズの最適化と ローションポンプ射出成形金型内の位置 モールドフロー解析によるシミュレーション、解析、設計調整の体系的なプロセスが含まれます。この最適化を達成するためのステップバイステップのガイドは次のとおりです。
1. プロジェクトの目標と基準を定義します。
- ローションポンプ射出成形金型の目標と基準を明確に定義することから始めます。部品の品質、サイクル タイム、材料の使用状況、コストの制約などの要因を考慮します。
2. 材料データを収集します。
- 射出成形プロセスで使用される特定のプラスチック樹脂の正確な材料データを取得します。これには、メルト フロー インデックス (MFI)、粘度、熱特性、その他の材料特性が含まれます。
3. モデルの作成:
- キャビティ、コア、冷却チャネル、ランナー システムを含む、ローション ポンプ部品と射出成形金型の詳細な 3D モデルを作成します。モデルが意図した生産条件を正確に表していることを確認してください。
4. シミュレーションのセットアップ:
- モールドフロー解析ソフトウェアを利用してシミュレーションを設定します。射出圧力、温度プロファイル、冷却速度などの射出成形プロセスのパラメータを定義します。ゲートの位置と初期ゲート サイズを指定します。
5. 最初のシミュレーションの実行:
- 選択したゲートの位置とサイズを使用して、初期モールド フロー シミュレーションを実行します。充填時間、圧力分布、ウェルド ライン、エア トラップの位置などの結果を分析します。潜在的な問題や改善の余地がある領域を特定します。
6. ゲート位置の分析:
- 選択したゲート位置の適合性を評価します。キャビティのバランスのとれた充填、外観上の欠陥の回避、ウェルド ラインの影響の最小限化などの要素を考慮してください。必要に応じてゲートの位置を調整します。
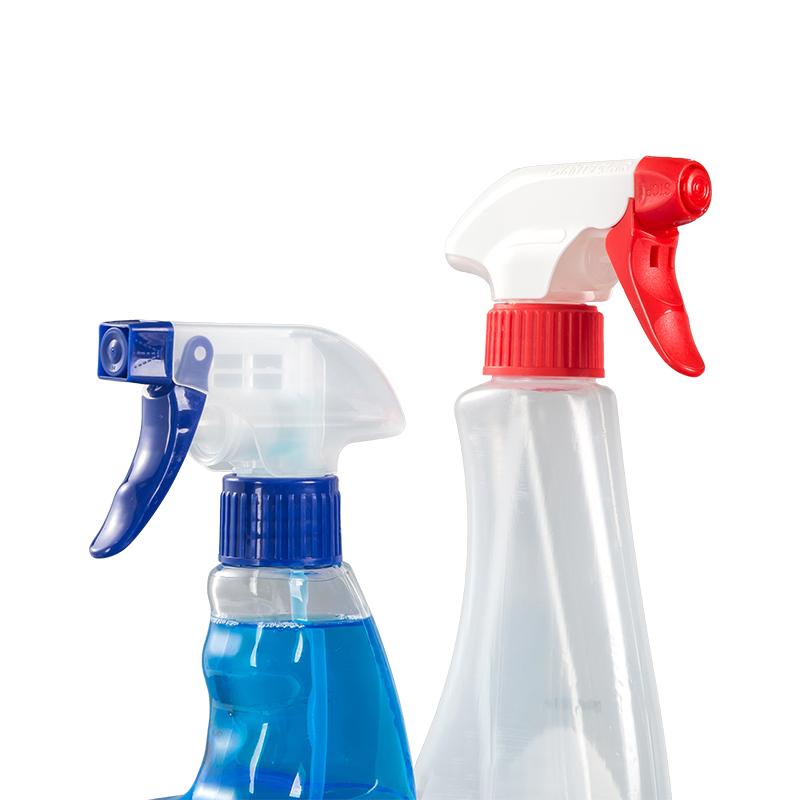
7. ゲート サイズの分析:
- ゲート サイズが射出プロセスに及ぼす影響を分析します。後続のシミュレーションでゲート サイズを徐々に増減して、欠陥を発生させずに充填時間、圧力、材料フローのバランスをとる最適なサイズを見つけます。
8. ゲートタイプの選択:
- ゲート サイズ解析の結果に応じて、スプルー ゲート、エッジ ゲート、ファン ゲートなどの適切なゲート タイプを選択します。ゲートのタイプは、材料がキャビティに入る方法に影響を与え、部品の品質に影響を与える可能性があります。
9. ランナー システムの最適化:
- ランナー システムの設計を最適化し、すべてのキャビティに材料が均一に分配されるようにします。ランナーの寸法と構成を調整して、材料の無駄と圧力損失を最小限に抑えます。
10. 冷却チャネルの分析:
- ゲートの位置とサイズが冷却効率に与える影響を評価します。選択したゲート構成が冷却チャネルの有効性を妨げないことを確認してください。必要に応じて、冷却チャネルの配置を調整します。
11. 反復シミュレーション:
- 反復シミュレーションを実行し、解析結果に基づいてゲートの位置とサイズを段階的に調整します。バランスの取れた充填や最小限の欠陥など、必要な基準が満たされるまで、設計の改良を続けます。
12. 最終検証:
- 最終的なモールド フロー解析を実施して、最適化されたゲート サイズと位置を検証します。設計が事前に定義されたプロジェクトの目標と基準を満たしていることを確認します。
13. 文書化と報告:
- 選択したゲート構成、シミュレーション データ、および設計調整を含む結果を文書化します。最適化プロセスとその結果を要約したレポートを準備します。